Hydraulic Suction filter is used primarily to trap and remove impurities from the hydraulic fluid. To ensure functional protection of the downstream pump, these should be directly installed into the suction lines of the pump, always below the minimum fluid level of the reservoir.
Hydraulic fluid is easily contaminated, mainly due to lack of initial cleaning and also due to external air, accidental ingression, and other particles which enter through the possible opening. It is for this reason, that fluid contamination starts prevalent upon the installation of new equipment.
During the initial "starting or breaking in" period, metal flakes from machinery can potentially damage the pump or other sensitive system components. As this fluid with such particles flows through the system, pump suction filters represent the “first-line” filtration and are often referred to as the Safety filter or pump protection filter. Choosing the right Suction Line Filter Element at this stage ensures a longer service life for downstream filters and critical components.
As this fluid with such particles flows through the system, Suction filters represent the “first-line” filtration and are often referred to as the Safety filter or Pump Protection filter.
The Purpose of Suction Filters is to:
- Prevents the entry of large-size solid contaminants into the hydraulic circuit
- Downstream filtration lifetime gets extended.
- Reduce the solid particle load on the finer filter, thereby extending service life intervals and facilitating reduced maintenance downtime.
- Avoid damage to the downstream fine filter from large solid particles such as iron fillings, and rust.
Suction filters need to be properly sized to avoid the cavitation of the pump. These filters are primarily suction filter for pump protection. The general oil cleanliness level required by the hydraulic system must be ensured by installing and using the appropriate filter for a given function, such as a Return or Pressure filter with the requisite degree of filtration fineness. The proper Suction Line Filter Element selection also plays a crucial role in achieving this cleanliness level efficiently.
Specifications of Suction Filters
- Inline or tank mounting filters
- Flow rates up to 1000 l/min
- Operating temperature range: -20 °C … +100 °C
- Recommended for use with mineral oil-based hydraulic fluids
- Numerous connection variants in the BSP thread (ISO 228) or NPT thread (ANSI B1.20.1) from 3/8” to 3”
- Magnetic bars can be provided for specific versions
- Integrated bypass valve of 0,2 bar (3 PSI) to reduce risks of high-pressure drops.
We propose from our principals and associates a wide range of high-quality, reliable, and cost-effective suction strainer for pump and suction filter assemblies. These are specially designed and engineered to protect the most important part of a hydraulic system—the hydraulic pump, which is the heart of every hydraulic system.
Short overview of possible suction filters for hydraulic applications:
Suction Strainers / Suction Filter elements
Pump Suction Filter elements are fully submerged filter elements mounted/installed on the suction line of a pump. These strainers feature a coarse mesh screen primarily designed to collect large solid particulates as the fluid flows into the pump. Suction strainers are widely used as they are simple, economical, easy to install, and housed within the reservoir, thus eliminating the need for any external work. Every Suction Line Filter Element is selected based on flow requirements and micron rating to match specific application needs.
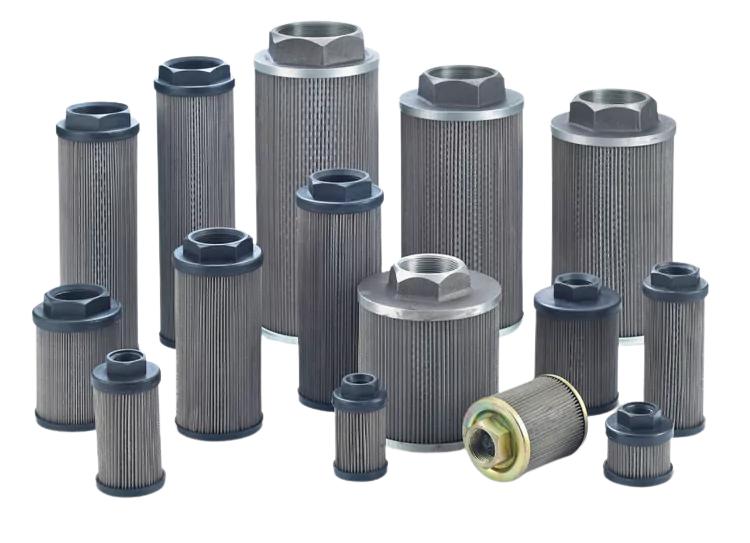
Commonly used variants are made with 125 & 149-micron wire mesh, but based on customer-specific needs, these can be made available in 50/63/74/100 microns filtration fineness. These suction strainer elements are available with or without a bypass valve and, if required, can be equipped with a magnetic column to facilitate retaining ferrous particles.
Spin-On Suction Filters
Spin-On type filters have an aluminum filter head with one or two spin-on filter elements. These are available with inline and flange mounting options, with inline mounting being the most common and preferred option. These filters offer easy servicing, fast and economical element replacement, and reduced maintenance costs. They are best rated to handle flow up to 150 l/min, covering a wide range of mobile and industrial applications.
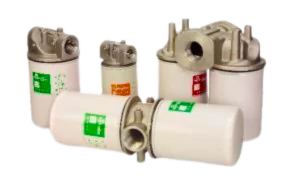
Suction Filter Assemblies
Applications with small tank reservoirs or pumps installed away from the reservoir necessitate the use of external filter housing. Inline mounting or Tank wall mounting suction filters are a possible solution for such cases. They can be used for a flow range of 500 to 700 l/min and can be equipped with a clogging indicator.
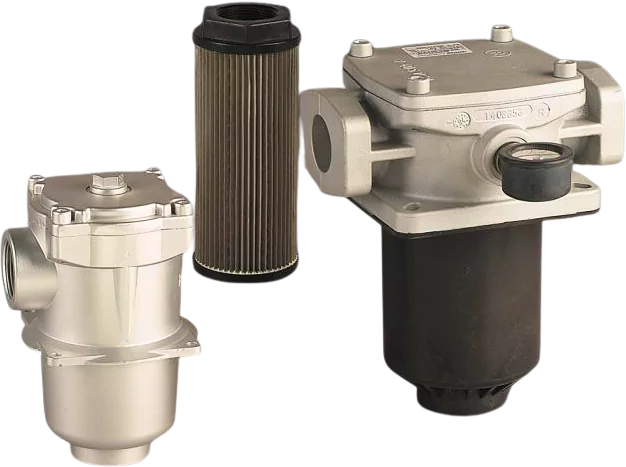