Hydraulic systems operate with continuous movement, leading to ongoing friction among their components. This friction inevitably causes wear and tear, ultimately contaminating the oil in use.
A significant 80% of system failures are attributed to or directly caused by oil contamination in hydraulic systems. These failures result in machine downtime, production delays, and financial losses. Taking proactive steps to address this issue involves implementing measures to control oil contamination.
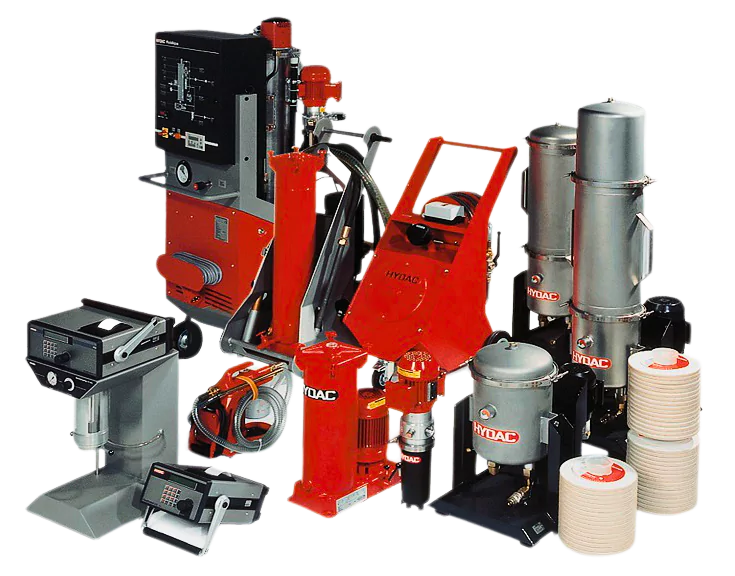
This includes identifying and monitoring sources of contamination while installing an effective Oil Filtration & Contamination Sensors system tailored to the system's components and operations. By integrating advanced filtration technology with precise oil contamination measuring sensors, significant benefits can be achieved in terms of increased productivity, enhanced machine uptime, extended equipment lifespan, and improved business profitability.
Oil Filtration & Contamination Sensors include
Oil Filtration units
- Portable and mobile oil filtration units
- Electrostatic oil filtration units
- Low vacuum dehydration units
Oil Contamination Measuring Sensors
- In-line oil particle counters for ISO/NAS measurement
- Automatic laser particle counters
- Aqua sensors/water content sensors
From offline filtration units for routine maintenance to continuous filtration systems for critical operations, our hydraulic oil filtration & contamination sensors solutions are designed to meet diverse requirements. With customizable options for filter media, flow rates, and filtration levels, our systems can be tailored to suit the specific needs of any application.
By maintaining the cleanliness of hydraulic fluids, our oil filtration & contamination sensors enhance the reliability and performance of hydraulic equipment. This results in reduced wear, minimized downtime, and optimized efficiency, ultimately maximizing the lifespan and productivity of hydraulic systems.
Contact us today to explore our hydraulic oil filtration & contamination sensors solutions and discover how we can help you to improve your equipment reliability, reduce downtime, and enhance operational efficiency.
Presenting our Portable Hydraulic Oil Filtration solution, transforming maintenance protocols in industrial settings.
Crafted for versatility and ease, our portable units excel in removing contaminants, preserving oil quality, and optimizing equipment reliability. These units are tailored for transferring hydraulic oils and purifying hydraulic systems.
Engineered for Maneuverability, they can be swiftly be navigated within the plant facilities, facilitating efficient maintenance, commissioning, and servicing.
Effective in removing contaminants from contaminated systems, these units restore lubricant cleanliness, minimizing component damage and enhancing equipment reliability.
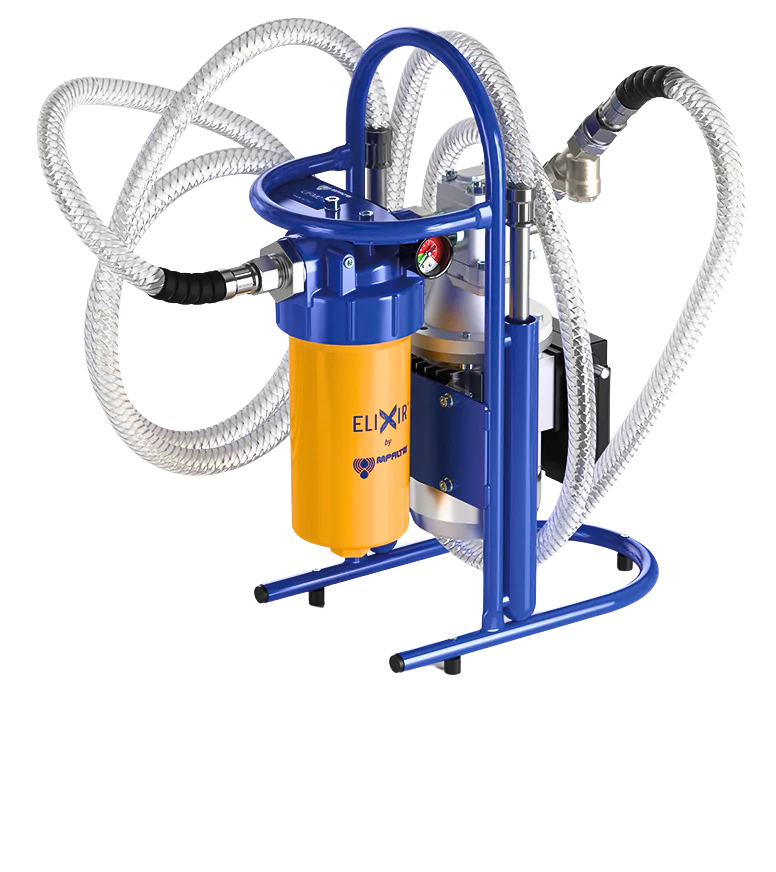
Product Specifications
- Operating pressure: 5 bar
- Flow rate: 10 to 15 lpm
- Pump type: Gear Pump
- Viscosity range: upto 100 cst (standard)
- Filter rating: 1 to 60 µm
- Filter materials: In-organic fibre, Wire mesh
- Weight: 18 kgs
Product Key Features
- Light and Portable
- Can be Hand lifted
- Compact Design
- Easy to maintain
- Spin-On Cartridges offer simple element replacement
- Easy and simple handling
In ensuring the performance and durability of machinery reliant on oil lubrication, an oil filtration unit is indispensable.
Mobile Filtration Units are meticulously designed to meet diverse hydraulic servicing needs, excelling in circulating and providing clean, filtered hydraulic and lubrication oils, essential for preserving critical system integrity and performance.
These units offer primarily mechanical filtration wherein the hydraulic oil is pumped through a filter, effectively capturing particles of various sizes for fluid cleanliness. Operating through off-line filtration, these system ensures lubricant cleanliness and equipment integrity, prolonging lifespan and optimizing performance.
Product Key Features
- Facilitates Oil Flushing during commissioning
- Achieves exceptional oil cleanliness ratings
- Oil Cleanliness Sensor can be be integrated
- Ensures prolonged working life of equipment
- Easy and simple handling
- Compatible with all conventional operating media
Product Specifications
- Operating pressure: upto 10 bar
- Flow rate: 20 lpm to 100 lpm
- Pump type: Gear Pump
- Viscosity range: upto 100 cst (standard)
- Filter rating: 3 to 100 µm
- Filtration stages: 1, 2 & 3
- Filter materials: In-organic fibre, Wire mesh, Paper, and Water-absorbent material
- Filtration type: Absolute or nominal filtration, depending on the filter material
- Weight:75 to 200 kgs
Engineered for comprehensive hydraulic maintenance and servicing, our Mobile Filtration
Systems optimize system performance, minimize downtime, and maintain oil integrity,
offering a cost-effective solution for long-term benefits.
Contact us today to explore tailored solutions for your specific application needs
and realize substantial cost savings over time.
Experience unparalleled performance and reliability with Electrostatic Oil Filtration Unit. Engineered to eliminate contaminants at submicron levels, it guarantees cleaner oil and extends equipment lifespan.
Operating on the principle of electrostatic separation, the unit applies high voltage (6 KV/ 12 KV) to attract charged particles towards electrodes. These impurities are then captured and removed, achieving cleanliness class 6-7 per NAS 1638 with regular use, without disrupting system operations.
- Removes contaminants at submicron levels.
- Capture particles regardless of shape, size, or material.
- Nominal oil flow rate: 2 to 10 lpm.
- Power consumption: 250 W to 550 W
- Low-cost spare filter paper consumables
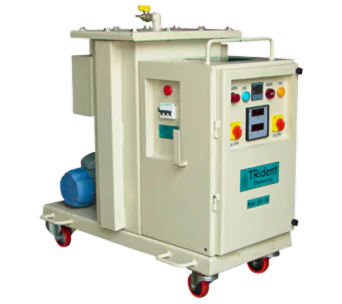
Use of Electrostatic Oil Filtration Unit on a continuous basis, tailored to the Hydraulic Oil tank volume, ensures cleaner oil, prolonged equipment lifespan, improved system efficiency, cost savings, and environmental sustainability.
Water presence within oil poses a significant hazard, hastening the process of acidification and leading to corrosion on component surfaces. This deterioration results in decreased load capacity, compromised temperature resistance, and hastened oil oxidation, ultimately translating into economic setbacks.
Introducing our state-of-the-art Low Vacuum Dewatering Unit, meticulously sourced from our esteemed principals and associates. Tailored to meet the diverse requirements of oil maintenance, lubrication applications, and hydraulic fluids in off-line filtration setups, this unit operates at lower vacuum levels, offering a cost-effective yet exceedingly dependable approach to oil dehydration across various industrial domains.
Operating on the principle of vacuum dewatering, the unit mildly heats oil within the range of 45 to 55 degrees Celsius within a vacuum extraction setup, effectively segregating free and dissolved water, along with free and dissolved gases, from hydraulic and lubrication fluids.
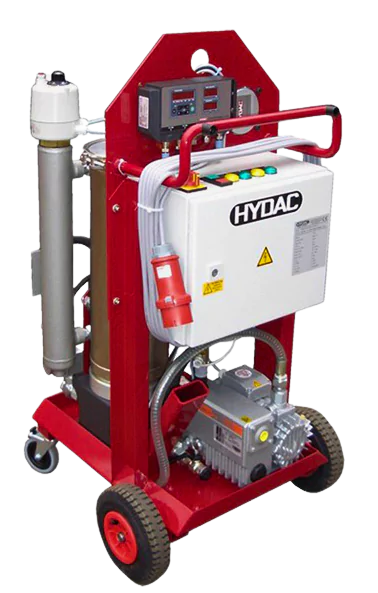
Salient Features
- Efficient removal of free and dissolved water, as well as dissolved gases, from oil.
- High contamination retention capability (up to 2.5 kilograms based on the filter element used)
- Operating pressure range: 0 to 6 kg/cm2
- Nominal oil flow rate: 6 to 20 lpm
- Pollution-free process devoid of any chemical reactions.
With our Low Vacuum Dehydration Unit, you can maintain oil integrity, minimize equipment downtime, and optimize overall system performance, thereby ensuring seamless operations and substantial cost savings in the long term.
Reach out to us today to discover how our solution can cater to your distinct application requirements.
The Oil Contamination Monitor stands as a vital tool for maintaining optimal performance and longevity in hydraulic and lubrication systems. Its primary function is to measure and analyze oil contamination levels, providing crucial insights into the cleanliness of the fluid.
The Oil Contamination Monitor employs advanced LED based Light Extinction Automatic Optical Monitor Technology to accurately measure and interpret the ISO/NAS cleanliness code level in real-time. Maintaining oil cleanliness within the specified ISO/NAS cleanliness code level is essential for ensuring smooth system operation and preventing component wear and damage.
By continuously monitoring the cleanliness of the oi and adhering to recommended levels, the operators can minimize the risk of costly downtime, extend equipment lifespan by enabling proactive maintenance strategies to be implemented, such as filtration and oil replacement, before contamination reaches critical levels.
Product specification, depending on the selected type
- Maximum operating pressure: 420 bar
- Measurement flow rate: 20 ... 400 ml/min
- Viscosity range: 1 ... 1000 mm²/s
- Media temperature range : -25 ..... +80°C
- Measures and Display format : ISO 4406, NAS 1638, AS 4059E.
- Communication options – RS485, MOBUS, CANBUS, 4…20 mA.
- Memory Data storage possible
- Relay function available in specific variants
- Compact design
- Light weight ~ 1.5 kgs
Contact us today to learn more about our Oil Particle Counter and discover how it can revolutionize your maintenance practices. Stay ahead of the curve, protect your investments, and optimize performance with precision maintenance solutions tailored to your needs
In the realm of fluid management, precision is of paramount importance. We offer Automatic Laser Particle Counter, designed to revolutionize contamination monitoring in hydraulic and lubrication systems. With advanced optics and detection capabilities, it accurately identifies and measures Solid particle contamination of various sizes.
Compliant with ISO 4406, SAE 4059, and NAS 1638 standards, it provides comprehensive insights into fluid cleanliness, thereby providing comprehensive insights into fluid cleanliness.
With cutting-edge technology and unparalleled accuracy, this advanced device sets the standard for precision monitoring, ensuring optimal performance and reliability.
Product specification, depending on the selected type
- Measures and Display format : ISO 4406, NAS 1638, AS 4059E
- Measurement range display: up to NAS 15 / ISO 25/23/21 / SAE 15
- Maximum operating pressure: 420 bar
- Measurement flow rate: 50 ... 800 ml/min
- Memory Data storage possible – 3000 to 4000 readings
- Viscosity range: 1 ... 400 mm²/s
- Media temperature range : -25 ..... +80°C
- Integrated, graphics-capable print
- Data output in the display or connection to a PC
- Communication options – RS232, RS485
- Robust design
- Unit weight ~ 10 to 15 kgs
Contact us today, to enhance your hydraulic unit reliability with precision monitoring solutions tailored to your needs.
Partner with us to safeguard your investments and unlock contamination monitoring processes to optimize performance and unleashing the full potential of your hydraulic and lubrication systems.
In hydraulic or lubrication systems, the presence of water can be detrimental, as it has the potential to acidify the oil, leading to compromised system operation. Therefore, it's crucial to monitor water content and address it promptly through effective filtration systems. Detecting water early on allows for proactive measures to prevent system malfunctions and damage, ultimately reducing downtime and ensuring smoother operations.
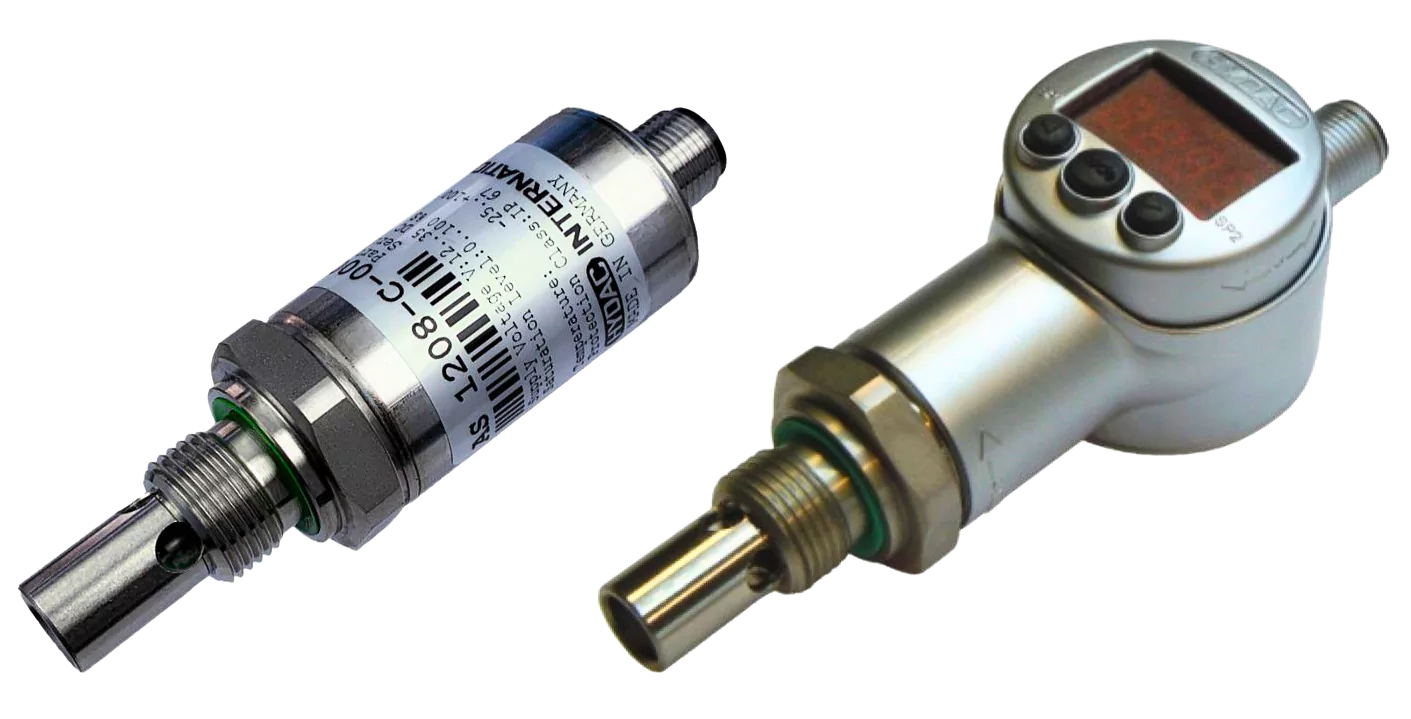
The most common methods for measuring water content are Parts Per Million (PPM) and Saturation level. While the PPM method is widely used, it is limited by its independence of operating temperature conditions, which can be a significant factor in hydraulic system applications. This limitation is addressed by Saturation level measurement, which adjusts for changes in operating temperature, providing a more accurate assessment of water content retention.
Aqua sensor sourced from our principals and esteemed associates, offers a solution for monitoring dissolved saturated water content in hydraulic oil. This sensor measures online, providing real-time data on the dissolved water content in terms of saturation level percentage. Importantly, it operates independently of oil type, age, and temperature. The saturation level percentage indicates the proportion of the maximum possible water quantity dissolved in the oil, with 0% representing water-free oil and 100% indicating oil completely saturated with water.
With our Aqua sensor, you can effectively monitor and manage water content in hydraulic oil, ensuring optimal system performance and longevity.